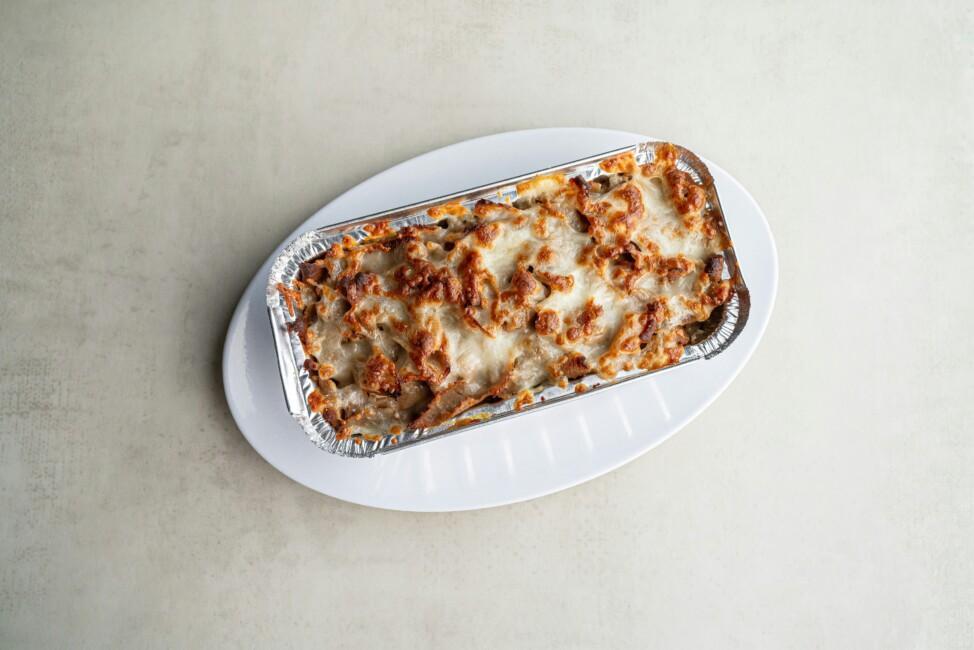
Key Considerations for Selecting Tray Packaging in Food Processing
Choosing the right tray packaging for food processing is a critical decision. It affects product safety, shelf life, and overall cost-efficiency. With so many options available, including thermoformed and stock packaging, it’s easy to feel overwhelmed.
This article breaks down the key considerations to help you maneuver through the decision-making process.
What is Tray Packaging in Food Processing?
Tray packaging is used in food processing to hold, protect, and display food products during production, storage, and retail. It is particularly prevalent in ready meal production, which often involves multi-component dishes such as pasta, rice, vegetables, sauces, and meats.
Tray packaging improves operational efficiency while ensuring food safety and portion accuracy, by offering a structured and secure way to manage and package these components.
Its design also aligns seamlessly with automated workflows for dosing, sealing, and secondary packaging, making it an integral part of modern food processing systems.
Key benefits of tray packaging highlight its value across multiple dimensions:
- Hygiene and Safety: Trays provide a protective barrier that shields food from contaminants, preserving freshness during production, storage, and transportation.
- Efficient Portioning: The structured design of trays supports precise dosing of ingredients, ensuring consistency in ready meal production.
- Convenience and Adaptability: Tray packaging is versatile, accommodating both solid and semi-liquid components, which is particularly useful for diverse ready meal recipes. Many trays are also designed to be microwave- and oven-safe, offering added convenience to consumers who seek quick and easy meal preparation options.
- Integration with Automated Systems: Trays are compatible with high-speed automated lines, facilitating seamless operations for dosing, filling, sealing, and labeling.
These features make tray packaging irreplaceable in food processing, as it effectively balances operational needs with hygiene, precision, and consumer convenience.
Tray packaging is a key element of modern food processing, combining safety, efficiency, and adaptability.
Common Types of Tray Packaging
1. Thermoformed Tray Packaging
Thermoformed tray packaging is a widely used solution in food processing, offering precision and versatility to meet the demands of diverse applications. It accommodates varying product types and production requirements while maintaining food safety and presentation.
Thermoformed trays are created by heating materials, such as plastic or bioplastics, until they become pliable, then molding and cooling them into specific shapes. This process allows for an exceptional degree of customization, making it well-suited for foods requiring precise portioning.
Multi-compartment trays are commonly used for ready meals containing components like pasta, rice, vegetables, and sauces, ensuring separation and an appealing presentation. Both solid and semi-liquid foods can be securely housed in these trays, which makes them ideal for a broad range of products.
This packaging type is especially effective for high-volume production because of its adaptability. Manufacturers can design trays in custom shapes and sizes to meet specific needs, from single-serving containers to elaborate multi-compartment configurations.
However, the initial investment for tooling and mold creation can be considerable, especially for custom designs. Additionally, lead times for developing new molds might impact production schedules, particularly when launching new products or updating packaging designs. These factors should be weighed carefully against the benefits of customization and efficiency.
Thermoformed trays combine durability, customization, and efficiency, making them irreplaceable for high-volume food processing.
2. Stock Tray Packaging
Stock tray packaging is a widely used option in food processing because of its practicality and accessibility. These trays are pre-manufactured in standardized sizes and designs, making them a versatile solution for various food applications.
They are particularly suited for ready meals that feature uniform components or simpler presentations, such as pasta with sauce combinations.
Because they are readily available, stock trays are ideal for meeting the demands of quick production cycles or smaller batch requirements.
The advantages of stock tray packaging make it appealing for businesses with specific needs. It is a cost-effective choice, especially for those operating on limited budgets or with lower production volumes.
Unlike custom packaging, stock trays do not require the creation of specialized molds, which significantly reduces upfront costs and lead times. Their compatibility with a variety of packaging systems for ready meals further improves their practicality.
There are important considerations to take into account. The standardized nature of stock trays limits customization, which can be a disadvantage for food products that require unique packaging designs or complex configurations.
Additionally, while functional, these trays might not effectively support brand differentiation or convey a premium image, which could impact consumer perception in competitive markets.
Stock tray packaging balances affordability with practicality, making it a key option for streamlined production needs.
3. Aluminum Tray Packaging
Aluminum tray packaging offers a combination of functionality and aesthetics that meets the demands of both producers and consumers. Its unique properties make it a practical choice for specific food applications, particularly for products that require high-temperature stability or enhanced product presentation.
Aluminum trays are lightweight and heat-resistant, making them ideal for oven-ready and reheatable meals. They are commonly used for foods such as baked pasta, lasagna, and other dishes that need to endure high temperatures during preparation or reheating.
Aluminum’s excellent thermal conductivity ensures even heat distribution, which helps maintain food quality and texture throughout the cooking process.
This type of tray also provides robust protection, safeguarding the contents from external contamination and physical damage during storage and transport.
However, they are typically not microwave-safe unless specifically labeled, which can limit their versatility for consumers who rely on microwave reheating.
Also, aluminum trays often come with a higher material cost compared to alternatives like plastic or cardboard, which could impact overall production expenses.
Aluminum trays combine heat resistance, durability, and recyclability, balancing functionality with premium appeal.
4. Cardboard and Paperboard Tray Packaging
Cardboard and paperboard tray packaging has become a popular choice in the industry because of its alignment with sustainability goals and versatility for various applications. These trays are crafted from renewable resources, such as wood pulp, and are often coated with moisture-resistant materials to improve performance.
They are particularly well-suited for packaging dry or lightly sauced meals, as well as fresh produce, making them a go-to option for brands seeking eco-friendly solutions.
One of the primary advantages of cardboard and paperboard trays is their environmental profile. These materials are biodegradable and recyclable, appealing to environmentally conscious consumers and supporting brands that prioritize sustainability.
Cardboard and paperboard are lightweight, which can lead to lower shipping costs and reduced environmental impact during transportation.
Their surfaces are also highly customizable, allowing companies to print designs, logos, and branding messages directly onto the trays to create a cohesive and attractive packaging solution.
But without specialized coatings, these materials have limited resistance to moisture and might not perform well with wet or heavy food items. Even with coatings, their structural strength is generally lower compared to plastic or aluminum trays, which could restrict their use in certain applications where durability is important.
Cardboard and paperboard trays balance sustainability with functionality but require careful assessment of their limitations.
5. Biodegradable and Compostable Tray Packaging
Biodegradable and compostable tray packaging offers a sustainable alternative to traditional materials, making it particularly relevant in a time of growing environmental awareness and regulatory pressures.
This type of tray is made from natural materials such as bagasse (a sugarcane byproduct), cornstarch, or polylactic acid (PLA), which are engineered to break down naturally in composting environments.
Their ability to decompose aligns with the increasing demand for eco-friendly packaging solutions in food processing.
These trays are commonly used for ready meals and single-serve portions targeted at eco-conscious consumers. They can accommodate a wide range of food applications, including solid foods and even some semi-liquid items when paired with appropriate barrier coatings.
This adaptability makes them a viable choice for businesses looking to balance sustainability with functional performance.
There are important considerations to weigh before making a purchase decision:
- Production costs are typically higher compared to conventional plastic or aluminum trays, which can impact overall profitability for food manufacturers.
- These materials often exhibit limited durability and heat resistance, making them unsuitable for applications like oven-ready meals or extended shelf-life products.
While these materials represent an important step toward more sustainable practices, they require careful evaluation to ensure they meet operational needs without compromising product quality.
Biodegradable trays offer sustainability but require trade-offs in cost and durability.
Key Factors to Consider When Choosing Your Tray Packaging Option
Factor #1. Material Selection Considerations
Selecting the right packaging material is important for ensuring the quality, safety, and appeal of food products. Material choice directly influences factors such as food compatibility, environmental impact, and consumer perception, making it a foundational consideration in food processing tray packaging.
Tray materials need to align with the specific properties of the food they are intended to hold. Wet foods, semi-liquids, and dry items each have distinct requirements.
For example, wet or semi-liquid foods demand materials with strong barrier properties to prevent leakage and contamination.
Similarly, trays for frozen meals have to endure low temperatures without becoming brittle, while those designed for reheating should be heat-resistant to avoid deformation or releasing harmful substances.
Sustainability is another critical factor, as both regulatory pressure and consumer preferences are increasingly driving demand for eco-friendly options.
For example, the European Union’s Single-Use Plastics Directive (SUPD) requires manufacturers to reduce the environmental impact of single-use plastics by transitioning to recyclable or biodegradable materials.
Recyclable materials like PET and biodegradable alternatives, such as compostable trays, help food processors meet these expectations while complying with such regulations.
Cardboard and paperboard trays, particularly those sourced from responsibly managed forests, offer a renewable option for packaging, aligning with both consumer demand and regulatory requirements.
However, the environmental impact extends beyond the tray’s disposal. The energy and resources required for production, along with the emissions generated, should also be considered when evaluating sustainability.
Tray materials have to satisfy food safety, functionality, and sustainability needs.
Factor #2. Production and Operational Factors
The ability of a tray to integrate efficiently into production workflows and meet the demands of scaling operations directly impacts overall productivity and cost efficiency.
One critical aspect is automation compatibility. Trays have to seamlessly align with automated systems used for dosing, filling, sealing, and packaging. Designs that allow smooth transitions and integration into existing production lines help reduce downtime and prevent interruptions.
High-speed production environments especially benefit from trays that maintain structural integrity and ensure consistent performance under rapid processing conditions. Selecting trays with these attributes minimizes errors while supporting streamlined operations.
Another key consideration is volume and scalability. The production scale often dictates whether thermoformed or stock trays are the more practical choice.
Thermoformed trays are typically better suited for high-volume operations that demand customized designs to accommodate specific product dimensions or branding needs. Their tailored nature allows businesses to achieve operational efficiency at scale.
On the other hand, stock trays are advantageous for smaller-scale operations or companies with diverse and frequently changing product lines. Their off-the-shelf availability provides flexibility and reduces lead times, ensuring quick adaptation to market demands.
The operational efficiency of tray packaging depends on its compatibility with automation and the scalability of production needs.
Factor #3. Meeting Hygiene and Safety Standards
Maintaining hygiene and safety standards is a non-negotiable priority in selecting tray packaging for food processing. Tray packaging has to uphold food safety regulations while protecting products during handling and transportation to ensure consumer health and product quality.
Regulatory compliance is a foundational consideration. Tray packaging materials have to meet the food safety requirements for the specific market, which can vary by region. Verifying certifications, such as those confirming that materials are food-grade and compliant with industry standards like FDA or EFSA guidelines, is important to avoid regulatory setbacks. Additionally, the tray design itself plays a role in maintaining hygiene.
Features that allow for easy cleaning and minimize the risk of contamination during production can help reduce food safety risks.
Durability under operational stresses is equally critical. Trays have to maintain their structural integrity through storage, transportation, and retail handling to prevent leaks, cracks, or other failures that could compromise hygiene.
Strong barrier properties are another important feature, as they protect food from external factors like moisture, oxygen, and contaminants, further safeguarding the product’s quality and safety.
Tray packaging has to meet both regulatory standards and operational demands to ensure food safety.
Factor #4. Cost and Consumer Appeal
When evaluating tray packaging options for food processing, cost and consumer appeal are two interconnected factors that can significantly influence decision-making. These considerations impact not only the bottom line but also the marketability of the product.
Budget plays a central role in determining suitable tray packaging.
Thermoformed trays, while offering customization and precision, often require a higher initial investment because of tooling and design expenses.
In contrast, stock trays are typically more affordable upfront, making them an attractive choice for operations with limited budgets or lower production volumes.
Beyond initial costs, per-unit expenses should be assessed in relation to production scalability. Higher volumes might mitigate the cost difference between thermoformed and stock trays, emphasizing the importance of aligning packaging choices with long-term production needs.
Additionally, precise portioning offered by certain tray designs can reduce food waste, leading to potential cost savings over time.
Consumer appeal is equally critical. Tray packaging that incorporates compartments or custom designs supports portion control while improving convenience for end users.
Such features are particularly relevant for pre-portioned meals or snack products, where ease of use can drive consumer satisfaction.
Materials and finishes also contribute to a product’s visual and tactile appeal. Clear trays highlight product freshness and quality, while printed designs add branding opportunities and differentiation on shelves.
For certain markets, packaging aesthetics aligned with premium or environmentally friendly values can further elevate the product’s perceived value. These design choices directly influence purchasing behavior and brand loyalty.
Balancing cost efficiency with consumer-focused design is important for effective tray packaging decisions.
Finntray: A Tailored Solution for Your Tray Packaging Needs
Selecting the right tray packaging is both a technical decision and a strategic one. The balance between materials, operational efficiency, compliance, and market appeal directly impacts product success and profitability.
Thoughtful consideration of these factors not only ensures functional performance but can also strengthen brand perception and consumer trust.
For manufacturers looking to streamline their operations, systems like Kometos Finntray offer a practical solution. Designed specifically for ready meal production, Finntray ensures accurate dosing and seamless integration with tray packaging, handling diverse materials like plastic, aluminum, and cardboard with precision.
Our solution simplifies production workflows while adhering to the highest hygiene standards, ensuring contamination-free operations. Whether you’re working with multi-component meals like pasta, rice, and sauces or need scalable configurations for growing demand, Finntray offers tailored options to enhance efficiency.
Contact us today to learn more about our capabilities!
FAQ
What is a tray packaging?
Tray packaging is a method used to hold, protect, and display food products during processing, storage, and retail. It is particularly suitable for multi-component ready meals, ensuring portion accuracy and maintaining food hygiene.
What is the difference between a case and a tray?
A tray is an open-top container used for portioning and presenting food products, while a case is an enclosed structure, typically used for bulk storage or transport of multiple trays or packaged items.
What is a PP tray?
A PP (polypropylene) tray is a type of tray packaging made from durable, heat-resistant plastic. It is widely used for ready meals due to its ability to withstand high temperatures, making it suitable for microwave and oven use.
What is a tray used for?
A tray is used to hold and protect food components during production, transport, and retail. It ensures portion control, maintains hygiene, and offers convenience for ready-to-eat or reheatable meals.
What is the function of plastic tray?
A plastic tray provides a durable, lightweight, and hygienic solution for holding and packaging food products. It protects the contents, enables precise dosing, and supports automated workflows in food production.