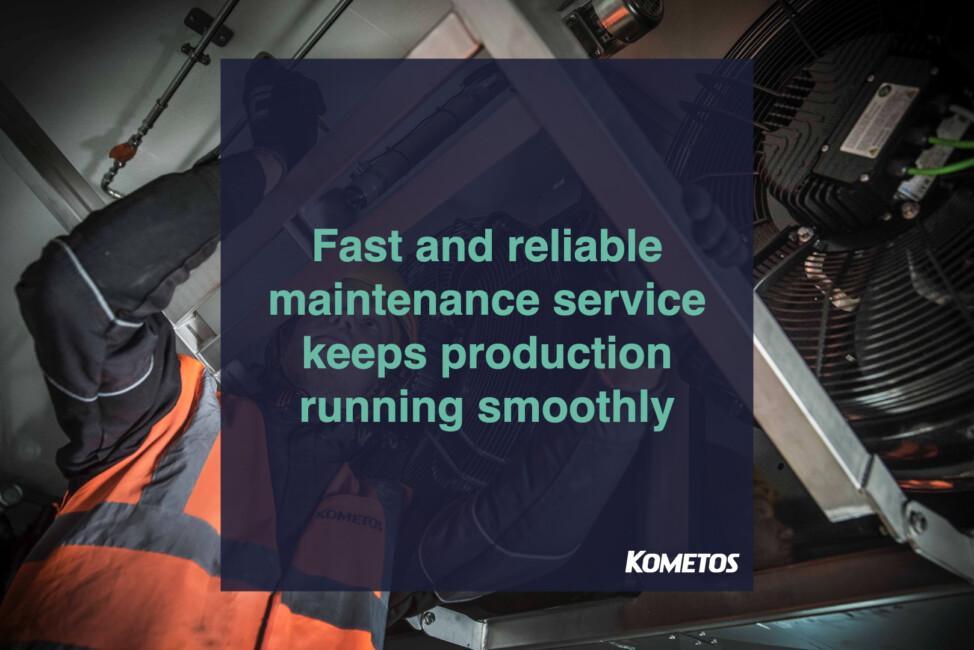
Fast, responsive, and reliable maintenance services ensure production continuity and avoid downtime
At the core of Kometos’s service promise lies the longevity of our high-quality production lines and equipment. Well-planned maintenance services ensure that our customers’ production facilities remain fully operational well into the future.
Quality maintenance and spare parts services are a key part of Kometos’s strategy
Kometos’s equipment delivery and after-sales operations go hand in hand. Customer service doesn’t end with order delivery, which is why the organization of high-quality maintenance and spare parts services is an important part of the company’s strategy.
The availability of spare parts and maintenance is crucial for uninterrupted operation of production facilities. Any spare parts or maintenance services needed are provided directly by Kometos.
Most spare parts are readily available in stock, ensuring quick deliveries. Additionally, Kometos’s extensive international network of suppliers ensures a comprehensive range of spare parts for by-order products. The most critical spare parts are kept on-site at the customer’s premises.
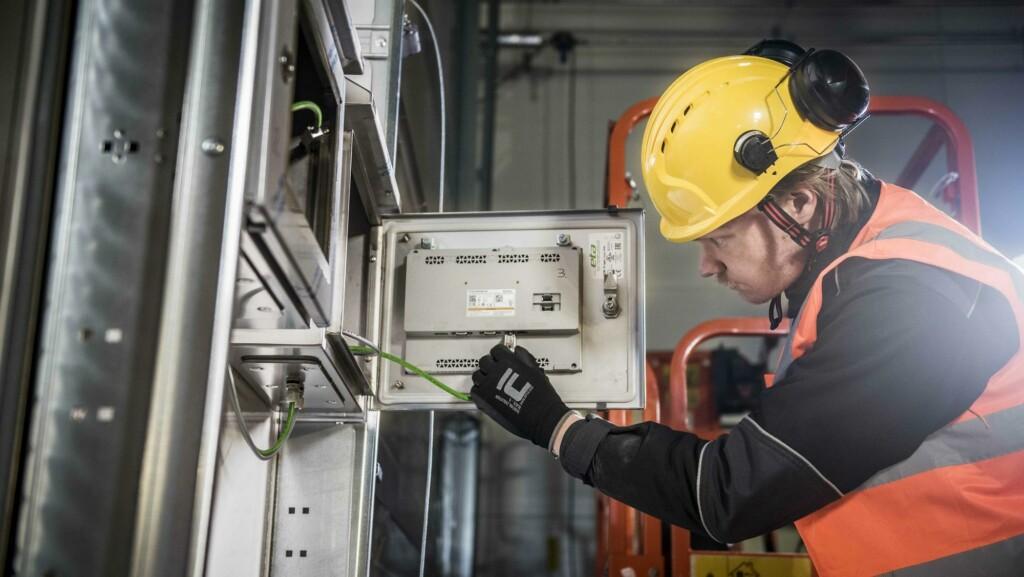
Quick response minimizes production downtime
In the food industry, it’s essential that production continues smoothly and without interruptions. In the event of a breakdown, maintenance must be on-site quickly. Therefore, Kometos responds promptly to service calls – maintenance arrives at the customer’s location no later than the next day.
Seppo Juntti, Kometos’s Maintenance and pare parts services manager, emphasizes the importance of quick response:
We consider ourselves successful when we have been able to assist our customers with maintenance and spare parts promptly and without production downtime.
Employee training boosts independence
Every delivery by Kometos includes training for operating and maintenance personnel.
The training covers thoroughly the operation and use of equipment. And of course, during maintenance visits, Kometos’s personnel can provide more detailed information about the equipment and production lines.
Even though Kometos’s maintenance service is always available to support customers, competent local operating personnel are the best guarantee for reliable operations and high customer satisfaction. Thorough onboarding provides staff with the skills necessary to use the lines efficiently and the understanding of when to alert Kometos if further maintenance is needed.
Continuous maintenance ensures the equipment’s longevity
Kometos’s maintenance contract covers much more than service requests in case of breakdowns. The agreement includes regular inspection visits to prevent breakdowns and production interruptions, as well as, if necessary, rapid on-site service and spare parts delivery.
Periodic inspection visits avoid safety and hygiene risks. Equipment is cleaned and re-insulated as needed, ensuring that production hygiene is maintained at the food industry’s required level. Regular inspection also detects potential safety risks, allowing proactive response.
Continuous maintenance aims for the longevity of equipment. Kometos’s modular solutions are designed from durable materials, and when well maintained, the equipment can remain operational for decades.
“Our equipment is designed for longevity. With Kometos’s comprehensive maintenance services and our efficient maintenance organization, we ensure trouble-free operation of the equipment far into the future,” summarizes Seppo Juntti.
💡 How could Kometos enhance your production processes? Learn more about our solutions here.